Corrective action examples encompass a wide range of measures that organizations and managers implement to address performance issues, non-compliance situations, or process inefficiencies. Corrective actions play an often vital role in maintaining quality control and fostering continuous improvement in the workplace.
This informative article delves into various corrective action examples, immediate corrective action instances, and illustrations of corrective actions for employees. Immediate corrective action examples can be helpful in understanding how organizations can engage in swiftly addressing significant problems or urgent matters that could impact an organization's operations, reputation, or compliance with regulatory requirements.
These types of corrective actions are often initiated when there is an imminent risk to employee safety, financial stability, or customer satisfaction. So, what is corrective action in the workplace? Examples of immediate corrective actions may include issuing product recalls due to manufacturing defects or halting production lines in response to identified hazards.
Another example of immediate corrective action is the reassignment of tasks or responsibilities when employees are found to be underperforming or engaging in misconduct. In these cases, management must often act promptly to prevent further damage to the organization's productivity and morale by meeting with the employee involved, discussing their performance concerns, providing support where necessary (e.g., additional training), and closely monitoring progress over time.
Examples of corrective actions for employees vary depending on factors such as the severity of performance issues, organizational policies, and applicable laws. One common approach involves implementing a progressive disciplinary process, through which employees receive increasingly severe penalties if their performance does not improve after multiple warnings and interventions.
In some cases, organizations may choose to administer more informal corrective measures before resorting to formal disciplinary proceedings. For instance, when a manager identifies minor performance discrepancies among team members - such as tardiness or failing to meet specific deadlines - they might have an informal conversation with the individual concerned about expectations moving forward.
When more serious performance issues arise—such as continuous failure to meet targets despite adequate training resources being provided—managers may utilize written warnings outlining precisely what needs improvement along with clear consequences if sustainable change is not achieved. Ultimately, in cases where employees consistently fail to demonstrate improvements or engage in severe misconduct—such as theft or harassment—organizations may need to consider summary or immediate termination.
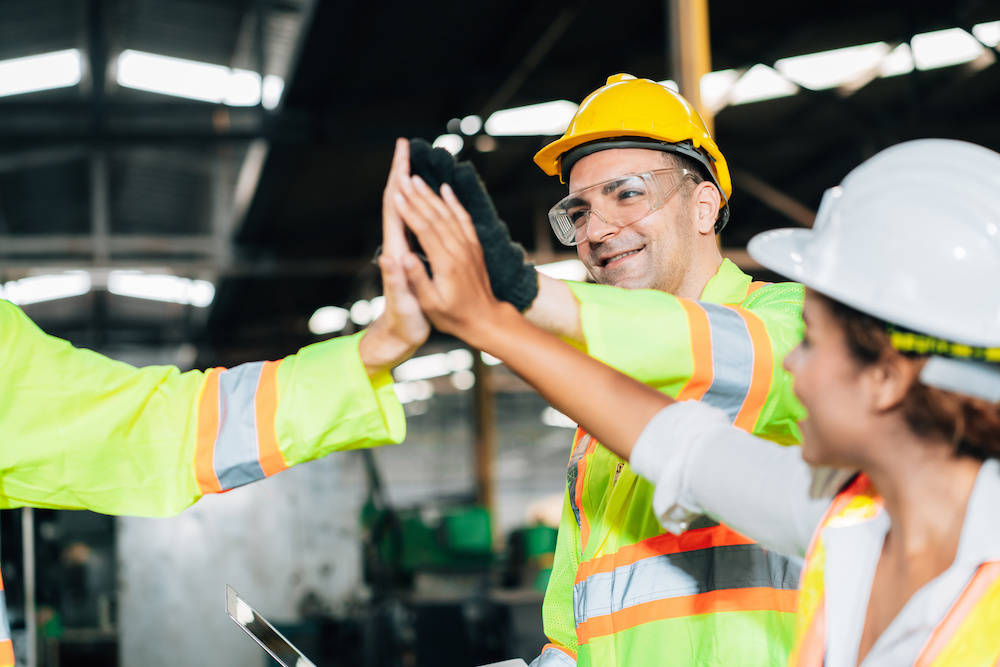
What Is Corrective Action And Preventive Action
Corrective action and preventive action (CAPA) is a systematic approach to identifying, evaluating, and resolving problems in various organizational processes. It encompasses measures taken to rectify existing nonconformities as well as addressing potential risks that could lead to future issues. CAPA often plays an integral role in maintaining compliance with industry standards, improving business operations, and enhancing overall customer satisfaction. In the workplace, corrective action serves as an essential tool for addressing performance gaps and ensuring adherence to company policies. It typically involves identifying the root causes of a problem, implementing a solution to resolve the issue, and monitoring its effectiveness over time. This process may include retraining employees on specific tasks or modifying work procedures to optimize productivity and minimize errors. Preventive action examples can range from conducting regular equipment maintenance checks to avoid malfunctions to implementing new safety guidelines following a near-miss incident. These proactive measures help mitigate potential risks before they escalate into more significant problems. An example of corrective action and preventive action working hand-in-hand can be seen in a manufacturing environment where quality control issues have been identified. Corrective measures may involve reworking defective products or removing them from the production line altogether. Simultaneously, preventive actions might include updating training materials or adjusting process parameters to prevent similar defects from occurring in the future. Another practical scenario could be within an organization's human resources department responding to employee grievances or workplace conflicts. Corrective actions here may consist of mediating disputes or enforcing disciplinary sanctions against employees who violate company policies. Preventative actions could involve organizing team-building activities, offering diversity and inclusion training, or revising workplace communication guidelines to create a more cohesive work environment. At the end of the day, understanding what is corrective action and preventive action is often crucial for organizations seeking continuous improvement in their processes. Adopting these principles allows companies not only to address existing issues but also anticipate potential disruptions and proactively tackle them before they materialize into significant challenges. As such, integrating the concepts of corrective and preventive actions often fosters a culture of self-assessment, learning, and growth.Types Of Corrective Actions
Corrective actions are an essential aspect of any organization's operations, as they focus on resolving problems and issues that have already occurred. This process helps to prevent the recurrence of such incidents, ultimately improving overall performance and efficiency. To better understand types of corrective actions, it can be helpful to delve further into some of them. To begin with, let's explore the most common types of corrective actions. These can be broadly categorized into three main groups: immediate, intermediate, and long-term corrective actions. * *Immediate corrective actions* consist of steps taken to quickly resolve a problem or issue at hand. For instance, isolating a defective product from a production line would be considered an immediate corrective action. * *Intermediate corrective actions* involve analyzing the root cause of an issue and implementing changes to prevent future occurrences. For example, if a manufacturing plant identifies that a particular machine is causing defects in products due to misalignment, an intermediate corrective action would entail adjusting the machine accordingly. * *Long-term corrective actions* are established by organizations to address systemic issues or improve overall operational effectiveness. These may include revising policies or procedures or investing in new technology or equipment upgrades. One industry where corrective actions are particularly crucial is manufacturing. Corrective action examples in manufacturing could include instituting regular quality checks on raw materials received from suppliers or implementing better training programs for employees handling sensitive equipment. It’s also important to differentiate between corrective action and preventive action. While both aim for improvement within an organization's processes and systems, their primary distinction lies in timing – corrective actions deal with existing issues while preventive measures focus on avoiding potential problems before they arise. To better understand how corrective and preventative action work together to create a safer work environment, it can be helpful to review the difference between corrective action and preventive action with examples. For example, suppose a company identifies that its current storage methods for hazardous materials are unsafe due to poor ventilation leading to potential accidents. In this case, it could take preventive action by consulting with relevant authorities, and modifying storage procedures before any accidents occur. Conversely, if an accident has already occurred due to the unsafe storage facility, the company would need to apply a corrective action—perhaps by relocating the hazardous materials, consulting with the relevant authorities, and ensuring proper ventilation in their new storage location.Corrective Action Response Examples
Corrective action response examples are often helpful to understanding an essential aspect of maintaining quality standards in various industries. Corrective action responses provide a structured approach to resolving problems or issues that have been discovered during audits, inspections, or other evaluation processes. By addressing these concerns promptly and effectively, businesses can ensure they maintain compliance with regulatory requirements while also improving overall performance. An often helpful component of corrective action responses is the identification of specific corrective action examples. These examples can serve as a guide for organizations on how to implement appropriate solutions to the identified issues. For instance, if an audit reveals that a manufacturing process is not meeting established quality standards, a corrective action example might involve retraining employees on proper procedures or updating process documentation. One important area where corrective actions are commonly employed is in response to a corrective action request. This type of request typically arises when an external entity such as a regulator identifies areas where an organization's operations do not meet established standards or requirements. In order to address these issues effectively, organizations generally need to develop detailed corrective action plans that outline the steps they will take to resolve the identified problems. These plans should include clearly defined goals and objectives, as well as timelines for implementation and completion. Preventive action examples in manufacturing are another helpful way to understand a vital aspect of maintaining operational efficiency and product quality within this industry sector. Unlike corrective actions which focus on resolving existing issues, preventive measures aim at identifying potential areas of concern before they become significant problems. By implementing robust preventive strategies, manufacturers can work to avoid costly disruptions due to non-compliance or poor-quality outputs. For example, one common preventive technique involves conducting regular inspections of machinery and equipment to detect signs of wear or damage early on. In doing so, repairs or replacements can be scheduled proactively before any major breakdowns occur. Similarly, implementing effective employee training programs can help improve overall knowledge and skill levels within the workforce – thereby reducing the likelihood of errors occurring in the first place. Both corrective action response examples and preventive action examples can help clarify the importance of these vital responses which are crucial components of an organization's overall quality management approach.Corrective Action Plan
A corrective action plan is an essential tool for organizations to address performance issues, improve employee behavior, and ensure compliance with established policies and regulations. It provides a structured approach to identifying problems, determining the root cause, and developing solutions that can be monitored and evaluated over time. This type of document often serves as a roadmap for both employer and employee to achieve desired outcomes by outlining specific steps required to rectify identified issues. One of the primary components of a corrective action plan for an employee is to provide specific examples of the problematic behavior or performance issues. Corrective action examples should be clear, concise, and detailed to ensure that the employee understands what needs improvement. These examples may include missed deadlines, violation of company policies, or failure to meet quality standards. By providing these instances in concrete terms, employees are better able to comprehend the severity of their actions and commit to making changes. To streamline the process of creating such plans, employers often rely on a corrective action plan template. This preformatted document typically includes sections for outlining the issue at hand, describing desired outcomes, listing potential solutions or strategies for improvement, assigning responsibilities for implementation and monitoring progress, setting timelines for review or completion dates, and documenting any follow-up actions required. Utilizing a template can be extremely helpful, not only saving time but also ensuring consistency across all corrective action plans within an organization. Implementing a comprehensive corrective action management system is crucial in addressing ongoing issues effectively. Such systems allow organizations to track employee progress in real-time while ensuring accountability throughout every step of the process. Still, it is important for organizations not only to develop but also meticulously monitor their corrective action plans through periodic reviews known as corrective action reports. These reports enable organizations to assess whether implemented solutions have effectively resolved employee performance issues or if further adjustments are needed. A well-devised corrective action plan serves as a valuable tool in fostering employee growth and development while ensuring adherence to organizational standards.Anvl: Let’s Get to Work
Ready to see how Anvl can impact your organization? Contact one of our experts today.